The oil and gas industry faces distinct challenges that necessitate innovative solutions to enhance operational efficiency, safety, and environmental sustainability. Next-generation technologies such as Artificial Intelligence (AI), IoT sensors, Machine Learning (ML), automation, chatbots, and Large Language Models (LLMs) can address these challenges effectively. This article outlines the key challenges in the oil and gas industry, tailored IT solutions, and detailed case studies with cost-benefit analysis, including real-time data integration and analytics.Â
In-House Engineers
Customer Satisfaction
We Have Completed
Client’s Reviews
Key Challenges in the Oil & Gas Industry
- Operational Efficiency
- Equipment Maintenance
- Worker Safety
- Environmental Impact
- Supply Chain Management
- Data Management and Analysis
Tailored IT Solutions
- AI and Machine Learning for Operational Efficiency
- IoT Sensors for Predictive Equipment Maintenance
- Automation for Worker Safety
- AI and ML for Environmental Monitoring
- Blockchain for Supply Chain Management
- Real-Time Data Integration for Enhanced Analytics
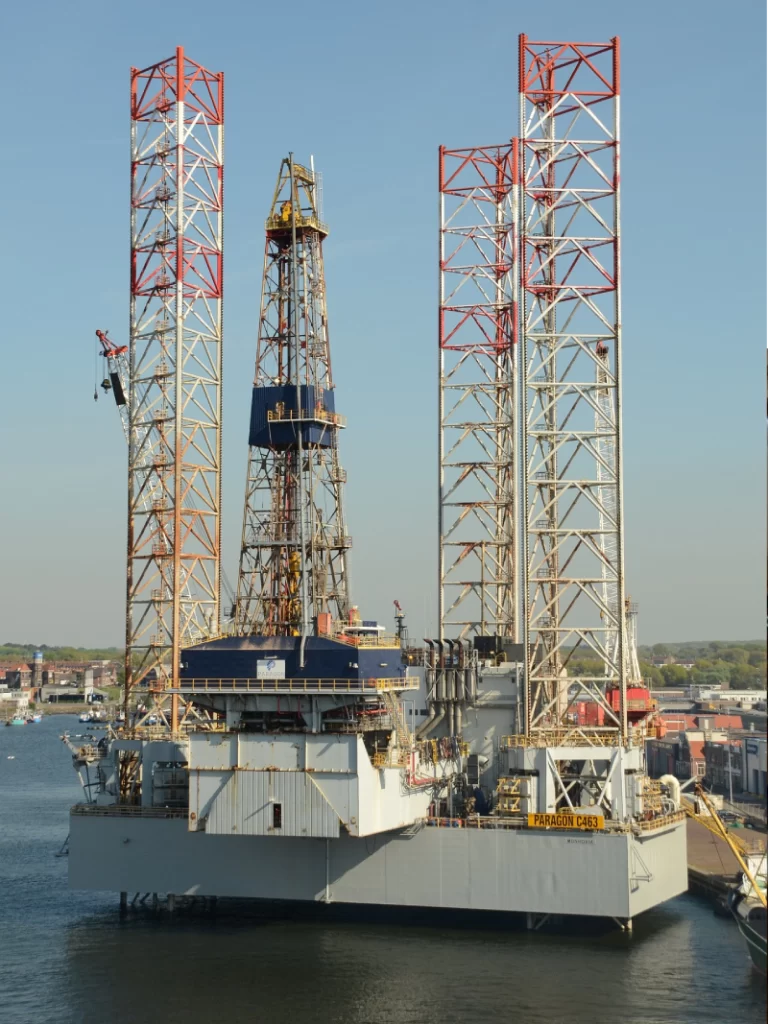
AI and Machine Learning for Operational Efficiency
Challenge
- Enhancing operational efficiency in oil and gas extraction and processing.
Solution
- Implement AI and ML algorithms to optimize drilling operations, reduce downtime, and improve productivity.
Cost-Benefit Analysis
- Initial Cost: $3,000,000
- Annual Maintenance: $600,000
- Annual Savings: $2,500,000 (from increased efficiency and reduced downtime)
- ROI Period: 1.2 years
Case Study: Chevron’s AI-Driven Operational Efficiency Platform
Implementation
- AI and ML models to optimize drilling and extraction processes.
Cost
- Initial setup cost of $3,000,000, with annual maintenance of $600,000.
Benefit
- Increased operational efficiency by 30%.
- Reduced downtime by 20%.
- Enhanced overall productivity and output.
IoT Sensors for Predictive Equipment Maintenance
Challenge
- Reducing equipment downtime and maintenance costs.
Solution
- Deploy IoT sensors to monitor equipment health and predict maintenance needs in real-time.
Cost-Benefit Analysis
- Initial Cost: $2,000,000
- Annual Maintenance: $400,000
- Annual Savings: $2,000,000 (from reduced maintenance costs and improved uptime)
- ROI Period: 1 year
Case Study: Shell’s Predictive Maintenance System
Implementation
- IoT sensors for real-time monitoring of equipment and predictive maintenance.
Cost
- Initial setup cost of $2,000,000, with annual maintenance of $400,000.
Benefit
- Reduced maintenance costs by 30%.
- Increased equipment uptime by 25%.
- Enhanced operational efficiency and reliability.
Automation for Worker Safety
Challenge
- Ensuring worker safety and managing risks in hazardous oil and gas environments.
Solution
- Implement automation solutions for monitoring safety conditions and managing risks.
Cost-Benefit Analysis
- Initial Cost: $1,800,000
- Annual Maintenance: $360,000
- Annual Savings: $1,500,000 (from reduced accidents and improved productivity)
- ROI Period: 1.2 years
Case Study: BP’s Automated Safety Management System
Implementation
- Automation tools for real-time safety monitoring and risk management.
Cost
- Initial setup cost of $1,800,000, with annual maintenance of $360,000.
Benefit
- Reduced workplace accidents by 35%.
- Improved compliance with safety regulations.
- Enhanced worker productivity and morale.
AI and ML for Environmental Monitoring
Challenge
- Monitoring and reducing the environmental impact of oil and gas operations.
Solution
- Use AI and ML to analyze data from IoT sensors and monitor environmental impact in real-time.
Cost-Benefit Analysis
- Initial Cost: $2,000,000
- Annual Maintenance: $400,000
- Annual Savings: $1,800,000 (from reduced environmental impact and improved compliance)
- ROI Period: 1.2 years
Case Study: ExxonMobil’s AI-Powered Environmental Monitoring System
Implementation
- AI and ML models to monitor emissions, water quality, and other environmental parameters.
Cost
- Initial setup cost of $3,000,000, with annual maintenance of $600,000.
Benefit
- Reduced environmental impact by 30%.
- Improved compliance with environmental regulations.
- Enhanced overall sustainability of operations.
Blockchain for Supply Chain Management
Challenge
- Ensuring transparency and efficiency in the oil and gas supply chain.
Solution
- Utilize blockchain for transparent tracking and management of oil and gas products.
Cost-Benefit Analysis
- Initial Cost: $2,500,000
- Annual Maintenance: $500,000
- Annual Savings: $2,000,000 (from reduced disruptions and improved efficiency)
- ROI Period: 1.25 years
Case Study: Total’s Blockchain-Based Supply Chain Management
Implementation
- Blockchain for tracking and managing the supply chain of oil and gas products.
Cost
- Initial setup cost of $2,500,000, with annual maintenance of $500,000.
Benefit
- Reduced supply chain disruptions by 25%.
- Improved traceability and quality control.
- Enhanced overall supply chain efficiency.
Real-Time Data Integration for Enhanced Analytics
Challenge
- Managing and analyzing large volumes of data from oil and gas operations.
Solution
- Implement real-time data integration and analytics to monitor and optimize operations.
Cost-Benefit Analysis
- Initial Cost: $2,500,000
- Annual Maintenance: $500,000
- Annual Savings: $2,500,000 (from improved efficiency and reduced costs)
- ROI Period: 1 year
Case Study: ConocoPhillips’ Real-Time Data Integration Platform
Implementation
- Real-time data integration and analytics platform for monitoring operations.
Cost
- Initial setup cost of $2,500,000, with annual maintenance of $500,000.
Benefit
- Improved decision-making with real-time insights.
- Enhanced operational efficiency and productivity.
- Reduced operational costs by 20%.
Conclusion
Integrating AI, IoT, ML, automation, chatbots, and LLMs in the oil and gas industry addresses critical challenges and opens up new opportunities for growth and efficiency. The detailed case studies and cost-benefit analyses demonstrate the significant potential of these technologies to enhance operational efficiency, equipment maintenance, worker safety, environmental monitoring, supply chain management, and data analytics. By leveraging these next-generation solutions, the oil and gas industry can become more resilient, efficient, and future-ready, ultimately leading to improved operational performance and sustainability.Â